According to modern human psychology, there are three possible responses to stress situations: flight, fight or freeze. In other words, in the case of a business-related problem, you can either evade it, tackle it or remain indecisive.
Edgar Koelewijn, Manager Data Governance at QSTA, is someone whose response falls into the second category. When he realized that new product introductions were at risk of being delayed due to long waiting times at GS1’s Data Management Services (DMS), he thought up a solution: to set up a highly efficient DMS of his own.
About QSTA
- Data Management Service (DMS) for the Food Industry
- Fully integrated with SyncForce Circular PIM
- Nationwide data quality checks
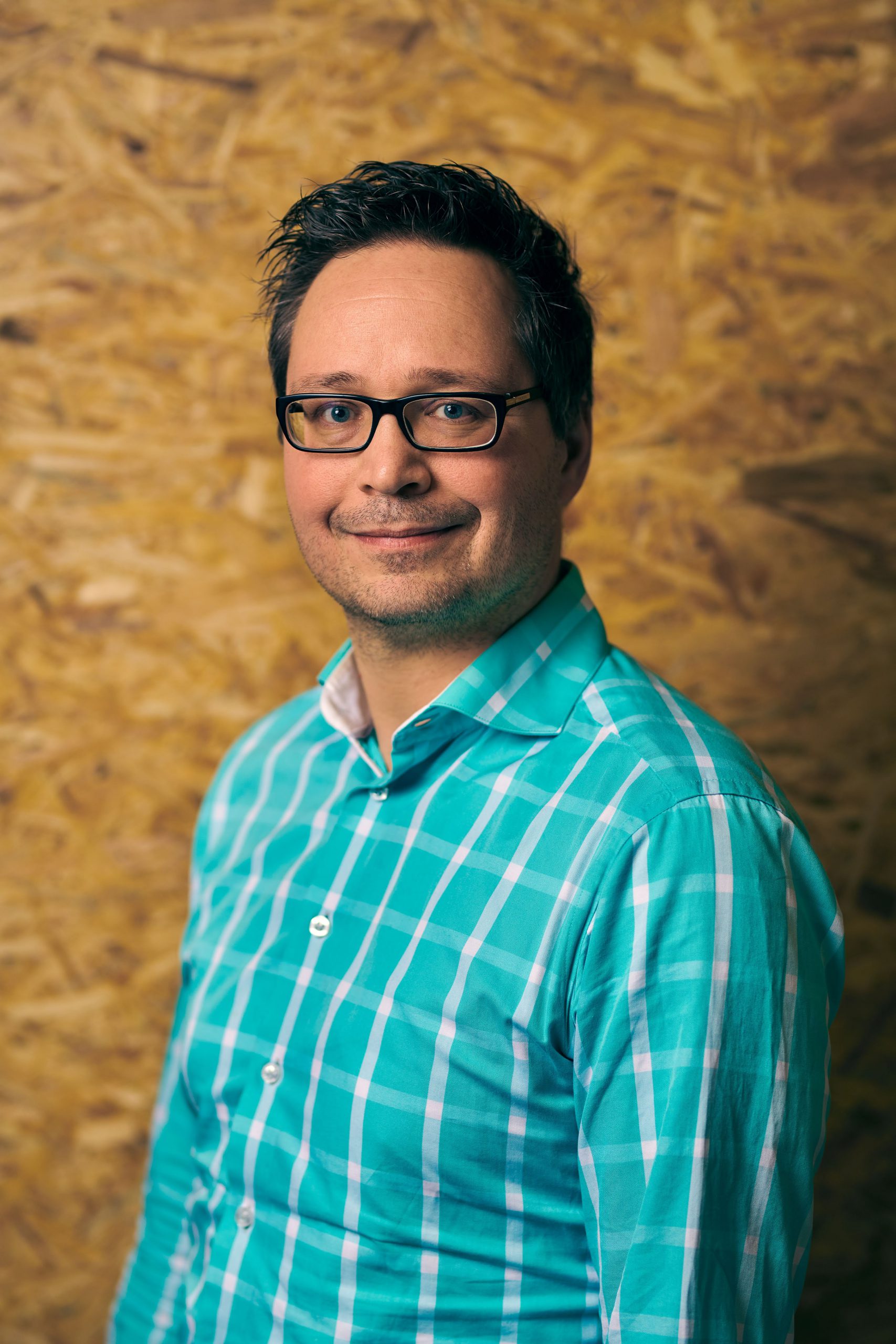
Long waiting times
Manufacturers who want their products to be added to the GS1 database have to arrange for a DMS to conduct a physical check of them, but limited capacity at the existing DMSs had resulted in long waiting times. At one point, it could take several months for a product to be approved. This was considerably delaying manufacturers’ new product introductions.
Let’s start our own DMS!
His idea was simple: if our products have to wait so long to be approved by GS1, let’s take matters into our own hands and launch a start-up – our own DMS! Besides assessing QSTA’s products, it could also approve products of QSTA Warehouse’s customers.
Just a couple of months after the initial idea, QSTA became a reality. The initiative achieved GS1 certification and is now available for use by any manufacturers in the Netherlands who want to add their products to GS1.
Nationwide checks
QSTA employees drive up and down the country to conduct checks in warehouses nationwide. Koelewijn: “This avoids manufacturers having to wait so long for the necessary check before their products can be listed in GS1. Thanks to optimizing the supply chain, we can perform an assessment within five working days.” Achieving that was not without its technological challenges, because the success of QSTA depended on Koelewijn and his team having access to data-checking software. “SyncForce provided the solution by helping to develop the Physical Data Quality (PDQ) checker based on SyncForce technology. Product manufacturers, using SyncForce Circular PIM, now have the option to use the QSTA Data Management Services (DMS).”
Unique player
“We’ve believed in this innovative initiative right from the start,” says SyncForce founder Hans de Gier. “At QSTA, they know how the food industry works. This has created a unique new player that can take care of the listing as part of the regular process, directly integrated with the SyncForce platform. This strategic partnership enables us to offer manufacturers an extra service, directly connected to QSTA.”
Koelewijn: “The thing we appreciated most in our collaboration with SyncForce was that they proactively advised us right from the start. Our idea was definitely not standard, and nor was the technical solution it required. SyncForce is clearly used to asking insightful questions and analysing processes as the basis for delivering the right technological solution. That really was an
impressive achievement.”
In the future Koelewijn hopes to be able to connect QSTA to other databases too, such as PS in foodservice and ImpactBuying.
Download testimonial
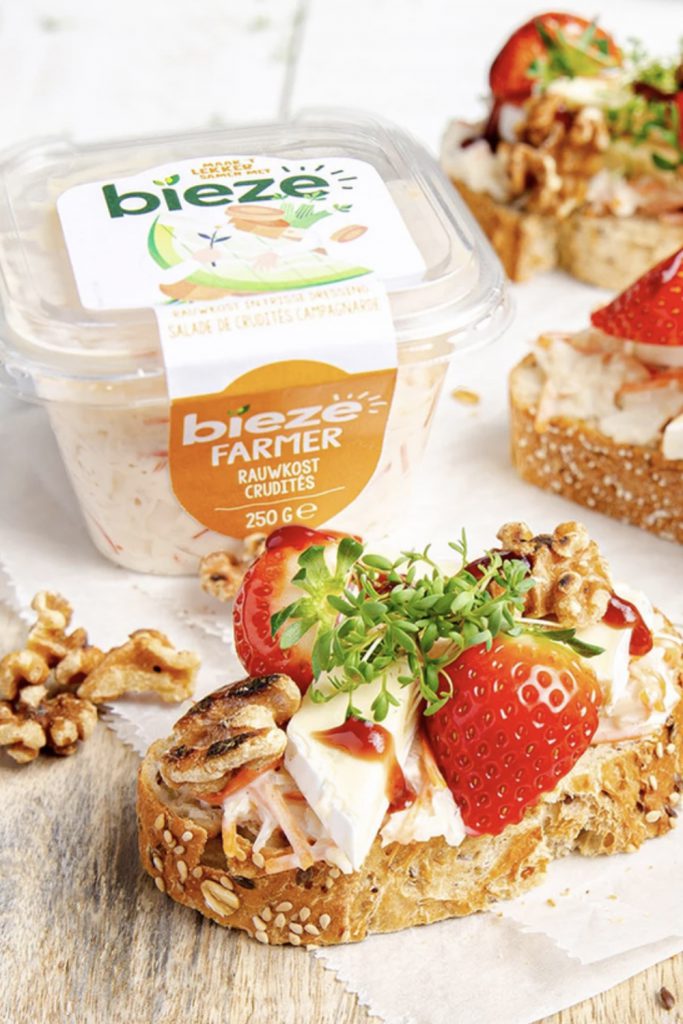